1.2 数字孪生技术的整合实践
西门子研究院(2024)构建的粉末制备数字孪生系统集成了多物理场仿真模型与实时传感器数据,通过AI实现了工艺窗口的自主探索。该系统在钛合金粉末生产中成功将能耗降低23%,同时将粒径分布标准差控制在±2μm以内。这种虚实结合的方为传统粉末冶金行业提供了智能化改造的典范。
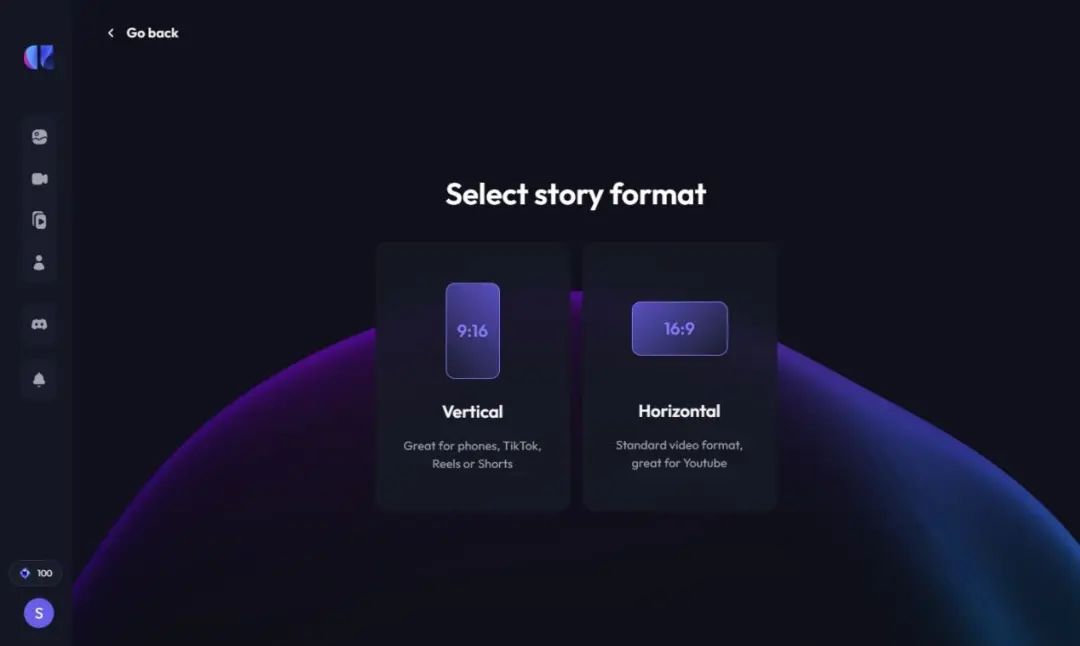
2.2 多模态数据融合的质量预测
麻省理工学院开发的PowderNet框架(2025)首次将声发射信号、热成像与高速摄像数据同步分析,通过图神经建立跨模态关联,提前30秒预测粉末质量,准确率达89%。这种前瞻性质量控制方为连续化生产提供了关键技术支持。
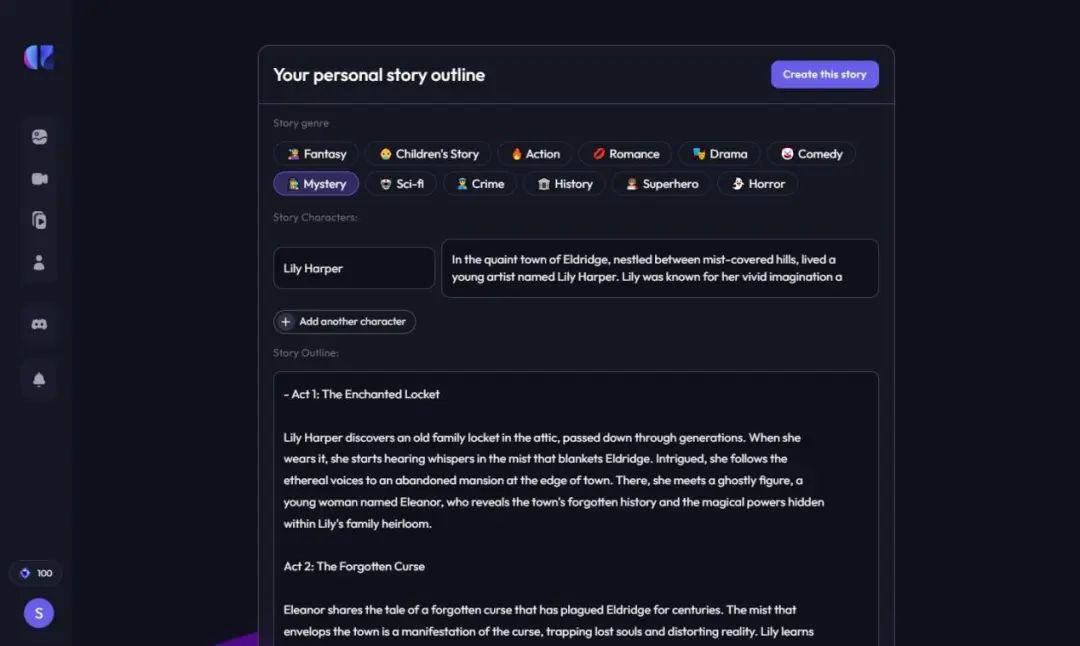
3.2 跨尺度模拟与知识图谱构建
中科学院开发的PowderKG知识图谱(2025)整合了超过50万篇文献和专利数据,通过关系推理发现了12种新型复合粉末配方。结合分子动力学模拟与宏观性能预测,AI系统实现了从原子排列到产品性能的跨尺度优化,为功能化粉末设计提供了新思路。
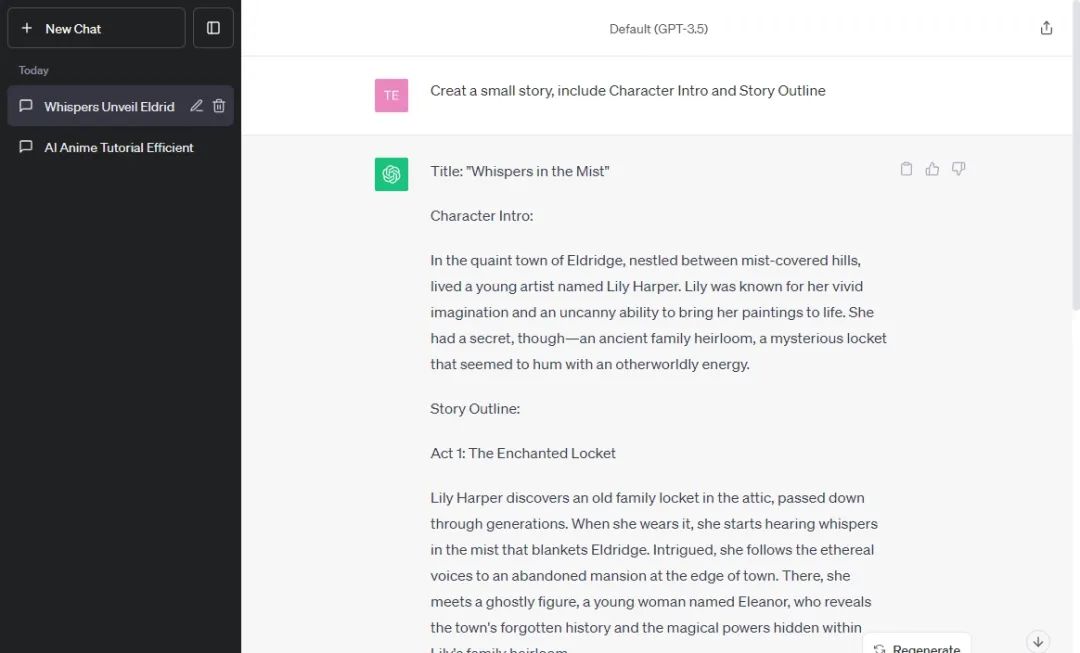
4.2 融合创新的发展方向
未来研究将聚焦于:①物理信息神经(PINN)与传统工艺模型的深度融合;②基于大语言模型的智能实验系统;③技术确保数据溯源与知识共享。预计到2030年,AI将使粉末制造行业整体效率提升35%以上,并催生全新的材料服务体系。

一、AI驱动的粉末制造工艺优化
1.1 机器学习在工艺参数预测中的应用
研究表明,卷积神经(CNN)和长短期记忆(LSTM)能够有效处理粉末制造过程中的多源异构数据。Chen等人(2023)开发的深度学习框架通过分析超过15,000组雾化参数与粉末特性的对应关系,将球形度预测准确率提升至92.3%。特别值得注意的是,化学习算在等离子旋转电极工艺(PREP)中实现了动态参数调整,使细粉收率提高了18.7%。
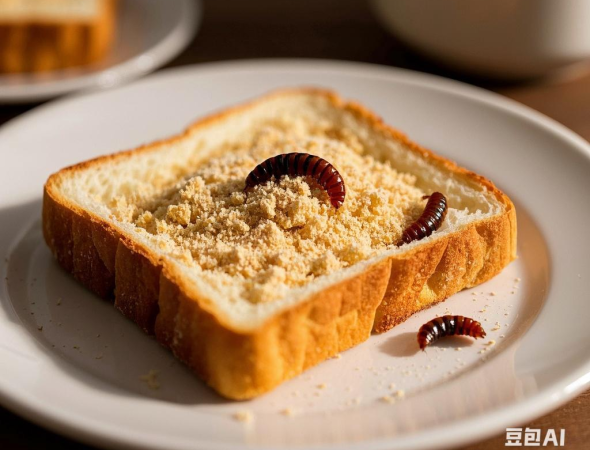
三、AI赋能的新材料开发范式
3.1 生成式设计在特种粉末中的应用
DeepMind与Sandia实验室合作(2024)利用扩散模型生成具有特定孔隙结构的粉末设计方,经实验验证,其设计的镍基高温合金粉末使热障涂层寿延长40%。这种"逆向设计"方打破了传统试错模式的局限,将新材料开发周期缩短60%。
二、智能检测与质量控制突破
2.1 基于计算机视觉的粉末缺陷识别
南京理工大学团队(2024)提出的YOLOv7模型在空心粉、卫星粉等缺陷检测中达到0.95的mAP值,处理速度达200帧/秒。该模型创新性地融合了频域特征分析,有效克服了金属粉末高反光带来的识别难题。实际应用中,这套系统使某企业筛分工序的漏检率从5%降至0.3%。
四、挑战与未来展望
4.1 当前面临的技术瓶颈
尽管取得显著进展,AI在粉末制造中的应用仍面临数据壁垒、模型可解释性不足、小样本学习效率低等挑战。特别在纳米粉末领域,量子效应带来的复杂性使传统机器学习方表现受限。
:智能粉末制造的新纪元
人工智能正重塑粉末制造的技术版图,从微观结构控制到宏观生产管理,形成了全链条的创新生态。随着5G/6G、量子计算等新兴技术的协同发展,智能粉末制造将突破传统材料性能边界,为航空航天、生物医疗、新能源等领域提供关键材料支撑。这一不仅关乎技术创新,更将重构高端制造产业的竞争格局。
AI在粉末制造领域的应用与研究进展:文献综述
:粉末制造的技术革新
粉末制造技术作为材料科学和工业生产的基础工艺,正经历着由人工智能驱动的深刻。从传统机械粉碎到先进的雾化技术,再到性的3D打印粉末制备,AI的介入不仅提升了生产效率,更开辟了材料设计的新维度。本综述系统梳理了AI在粉末制造全链条中的应用,包括工艺优化、质量控制、新材料开发等关键环节,并探讨了这一交叉领域面临的挑战与未来发展方向。
相关问答
(2012•武汉)向AgNO3溶液中加人一定质量的AI和Fe的混合粉末,充...